Hose Test Rigs for the Motorsport Industry
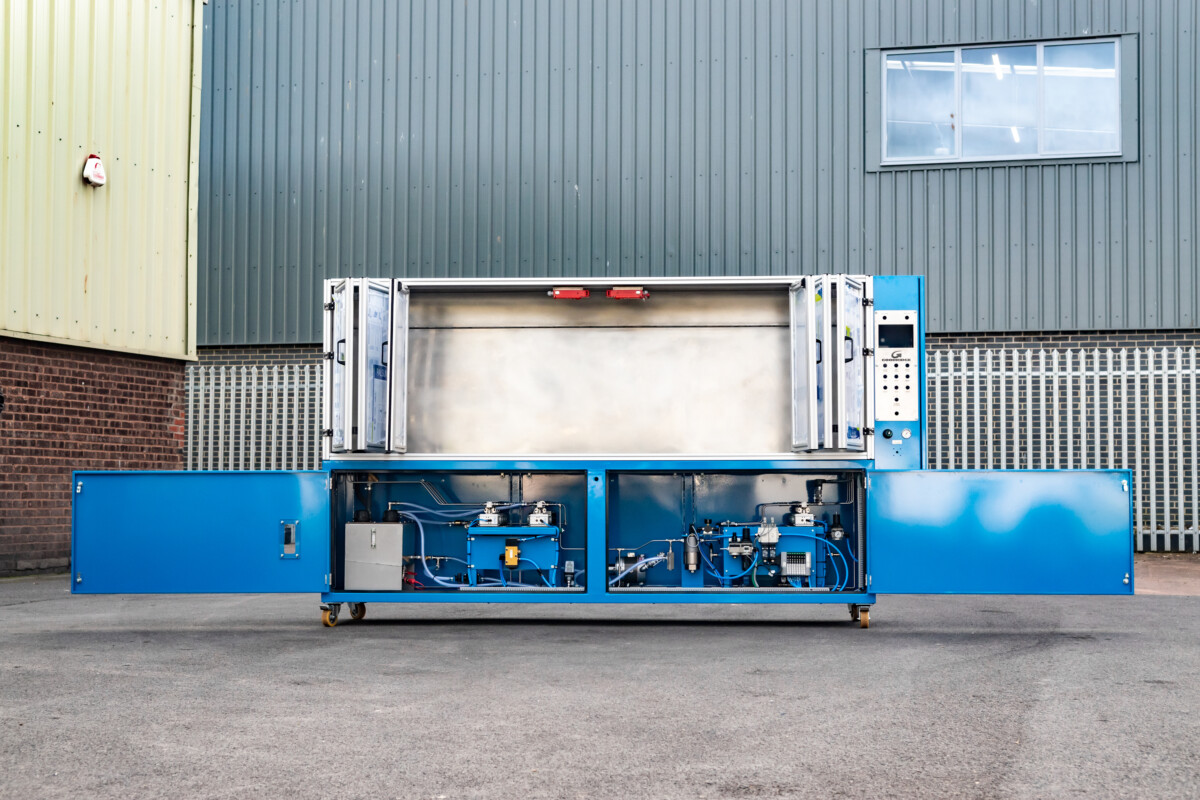
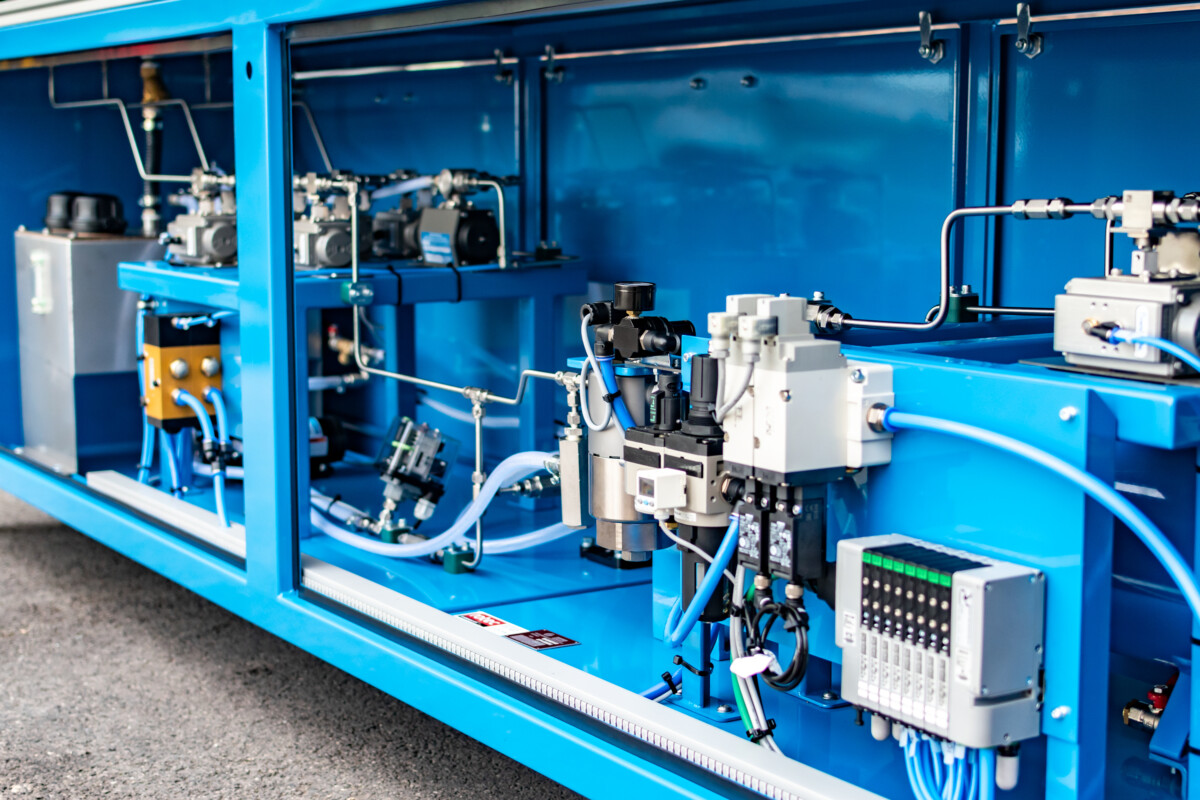
Rotec Hydraulics Ltd designed, built and commissioned two identical hose test rigs for a UK manufacturer who supplies world-leading racing teams with fluid transfer assemblies, hose and fittings.
UKCA/CE certificated and labelled, the test rigs are designed to provide regular and rigorous testing for a variety of flexible hose assemblies. The rigs were based on an existing design, but updated and improved due to the obsolescence of some of the components.
Measuring over 3 metres in length, the main capabilities of the test rigs include:
- Testing hoses up to four hoses at a time
- Testing hoses up to 250bar pressure using water as the medium.
- An air supply is used to control the hydraulic (water) valves and is used to pressurize the water using a 60:1 air/water intensifier.
- A low-pressure pump provides a means of flushing and pre-filling the hoses under test.
- Clean, filtered and dried compressed air supply of guaranteed continuous pressure of 6 bar minimum.
- Power supply of 240VAC 1 PH 50Hz 16A maximum for UK use.
- Nominal test sequence, based on existing rigs, (i.e., prefill/flush, test, vent, purge).

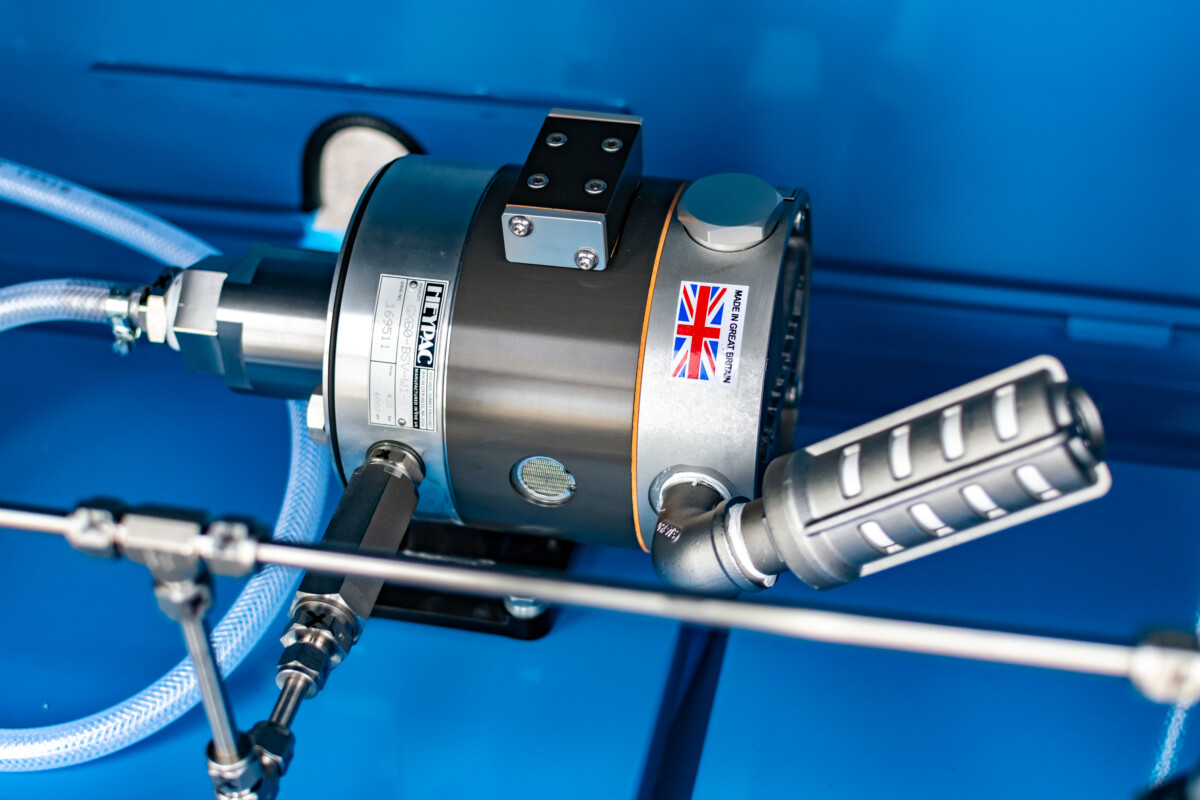
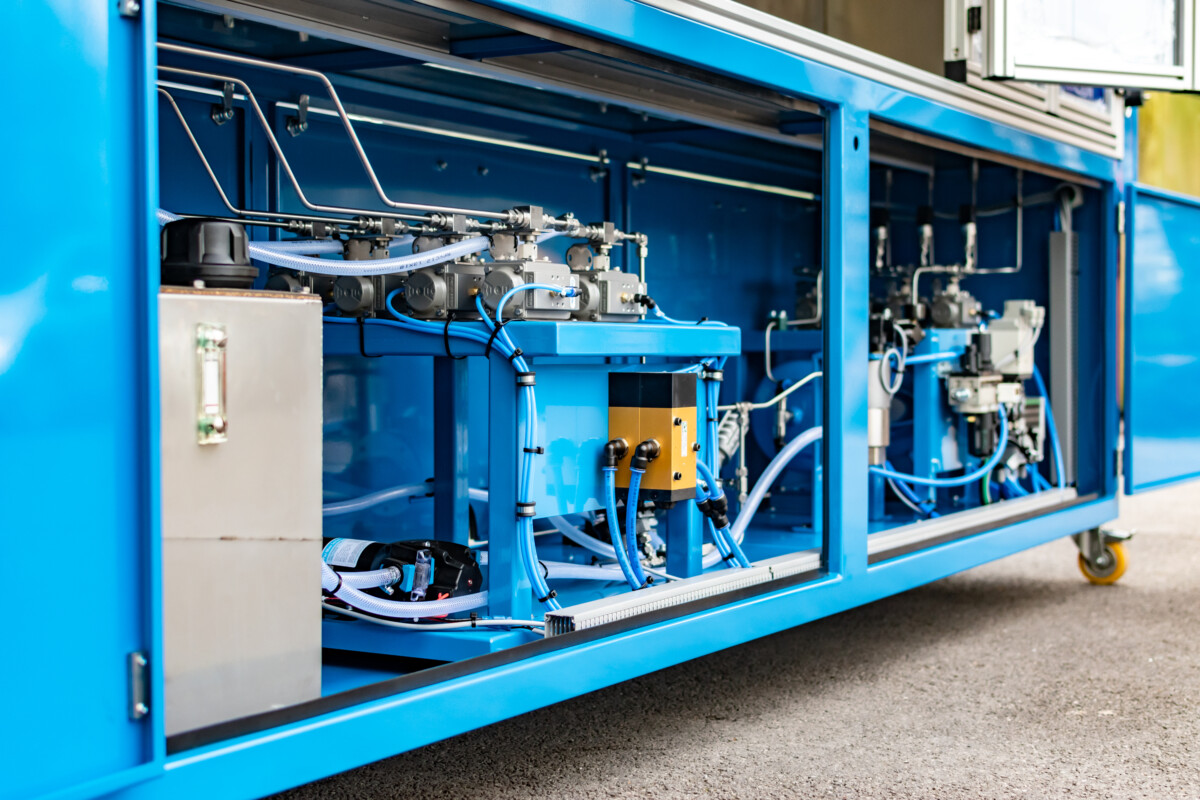
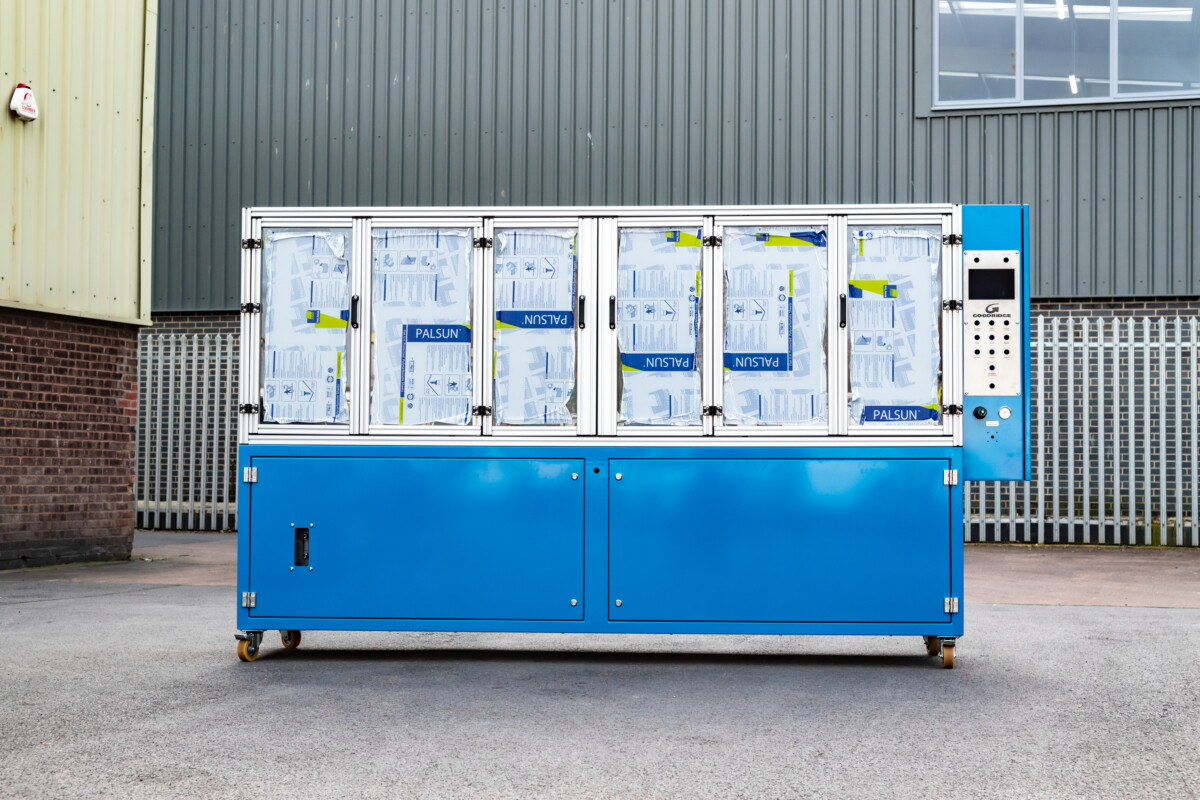

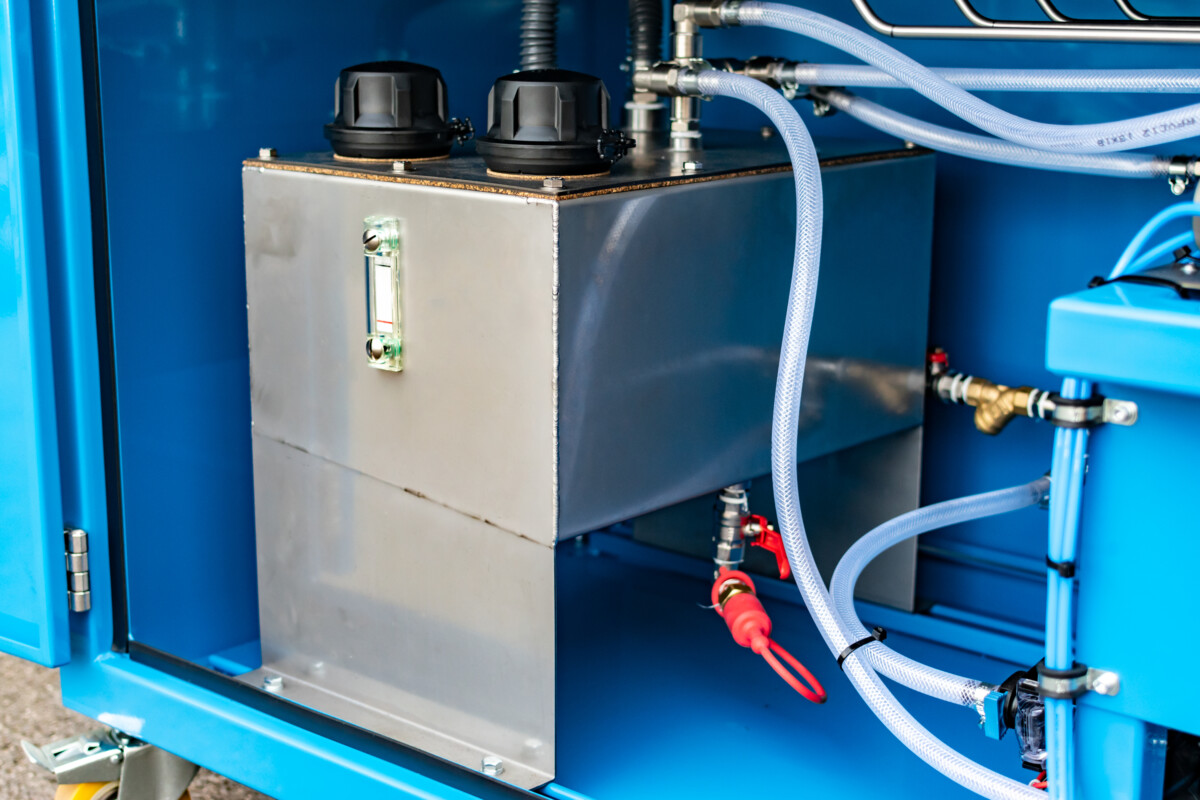
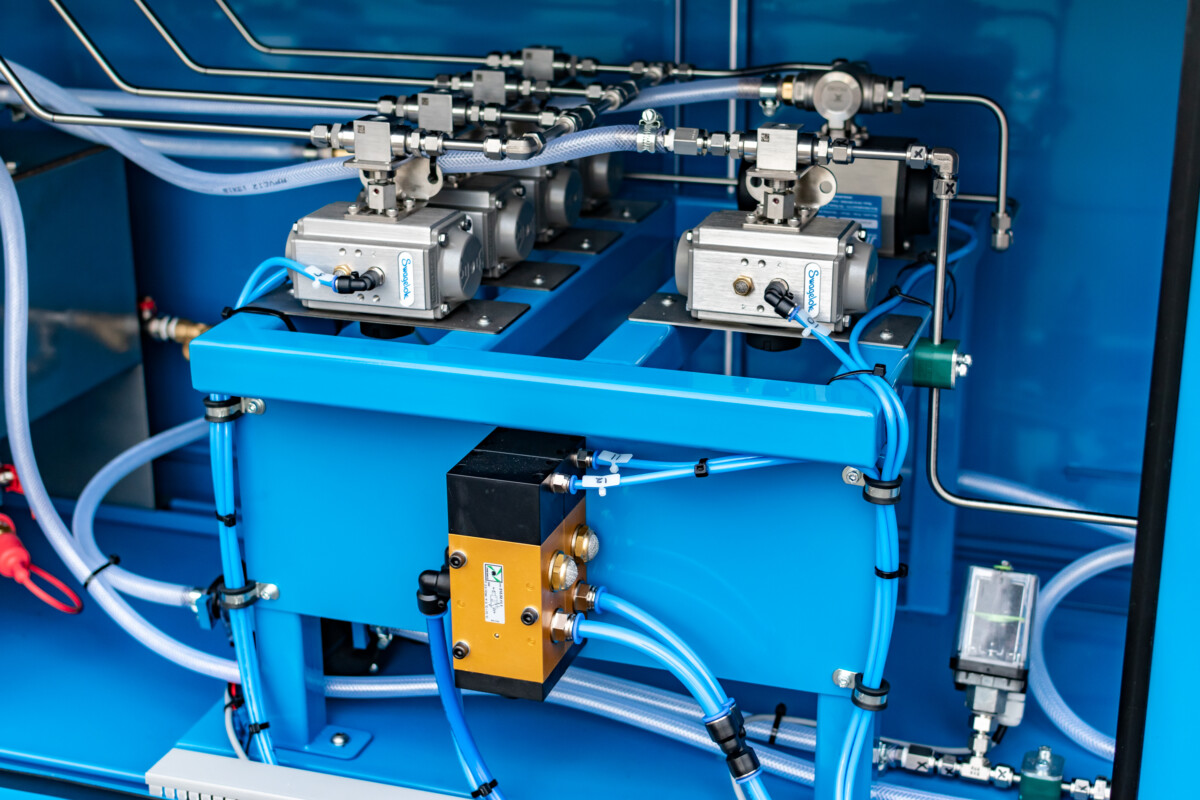
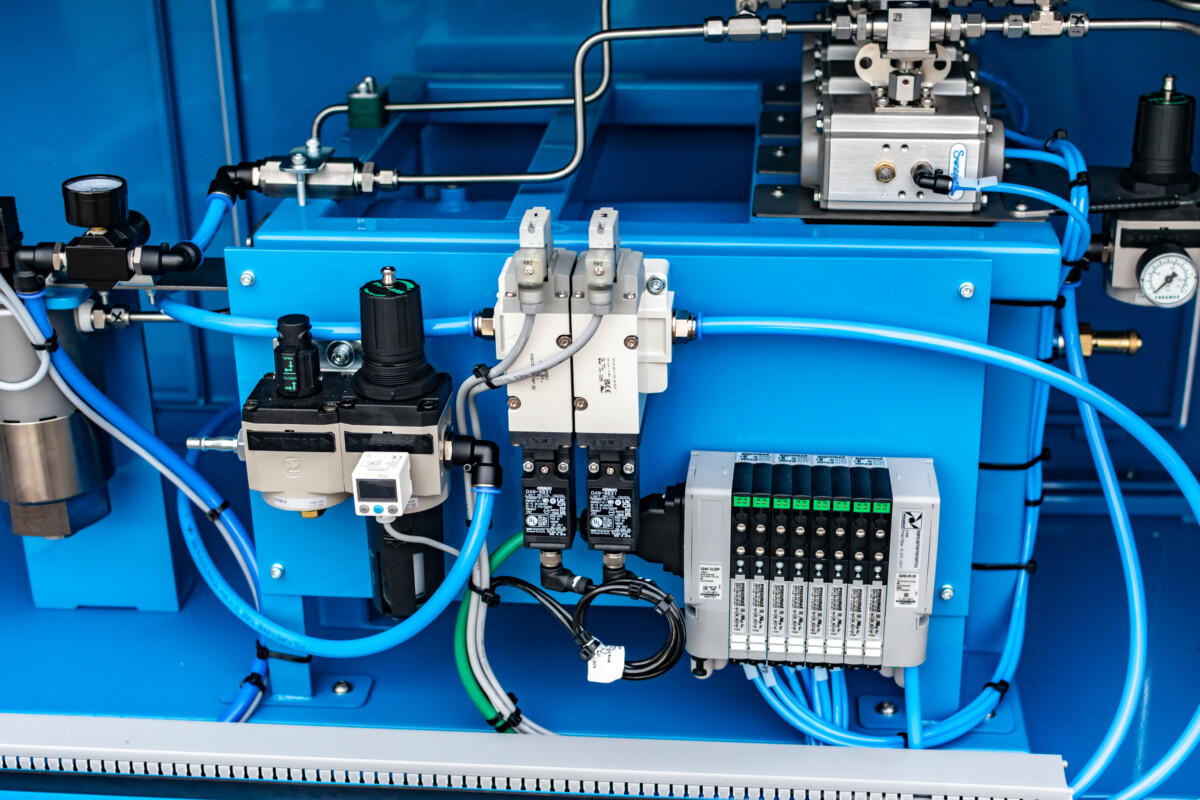
Each rig consists of a grade 316 stainless-steel upper half, and a powder coated steel lower half and electrical enclosure.
The lower half consists of the water reservoir, an air tank, an intensifier, a low-pressure pump, pneumatically operated hydraulic valves and a pneumatic control system. All the valves, which water flow through, high-pressure pipework & reservoir are made of grade 316 stainless steel to prevent corrosion. There are two lockable hinged doors on the front and three lockable panels on the rear to allow access for maintenance as well as internal led strip lights for enhanced lighting.
Inside the upper enclosure are eight ½” BSP ports (four either end) to which up to four hose assemblies can be installed for testing at up to 250 bar pressure. Bi-fold doors with transparent windows are fitted to enable access to the hoses, the doors are fitted with interlocks to ensure they cannot be opened whilst the hoses are under test. Internal led strip lights are built into the top of the enclosure to provide enhanced lighting. There is also a water filling point and drain which connect to a reservoir in the lower half of the rig.
Attached to the right-hand side of the rig is the Rotec designed lockable electrical enclosure which houses the customers electrical components. On the front face of the enclosure are controls for adjusting the test pressure, starting/stopping the testing cycle as well as an information screen displaying the results of the testing.
2 manually operated panel mountable air regulators were incorporated into the design. One is set and locked at 4.2bar inside the lower area (i.e., beyond the reach of the operator), the other panel mounted in the user control panel. This second unit is fed from the outlet of the former, ensuring the user cannot inadvertently set the test pressure to rise above the setting of the former and thus inadvertently (or intentionally) over-pressurise the system.
Rotec’s customer said:
“I am very pleased with the finished machine. As I expected, everything has been finished to a high standard.”
If you are interested in a similar project or any hydraulic power systems, do not hesitate to contact the team today on 01823 348900 or email sales@rotec.net.