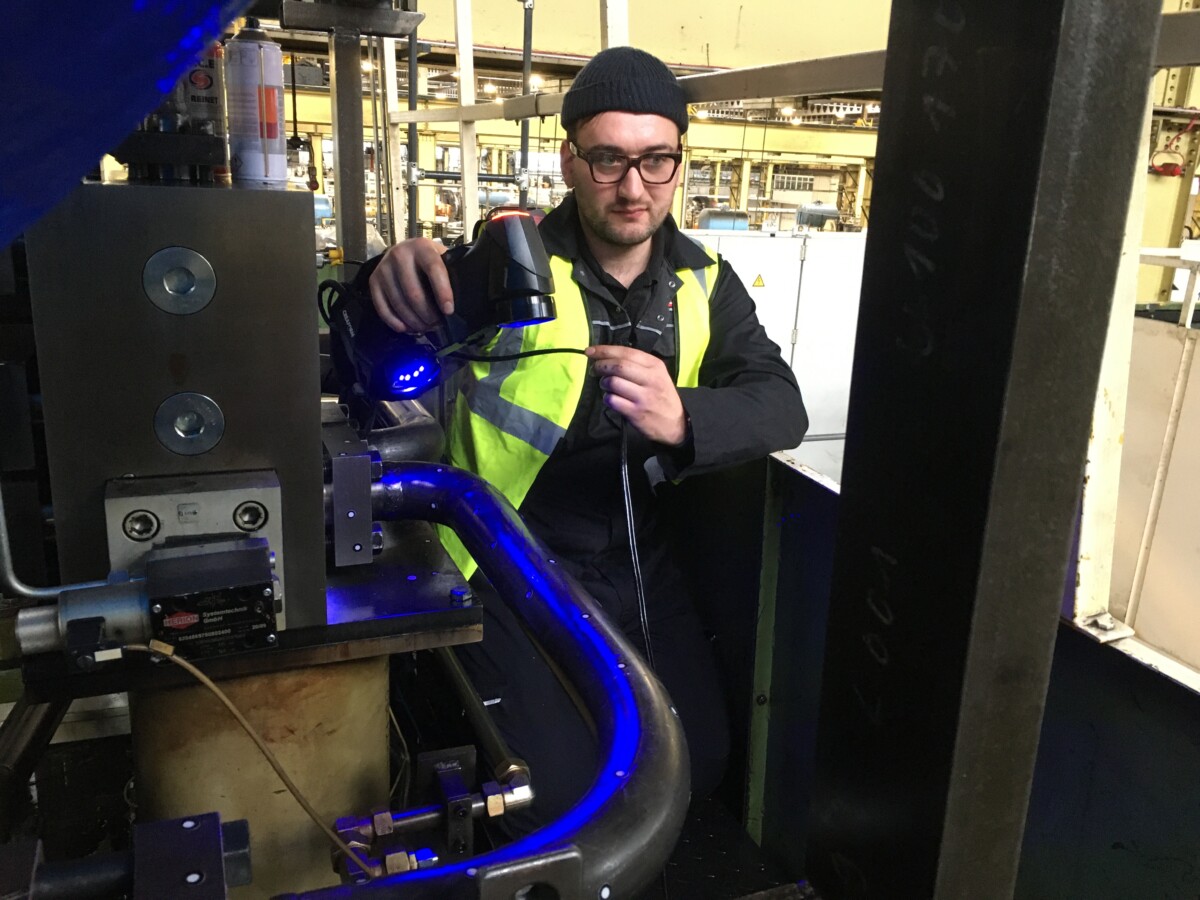
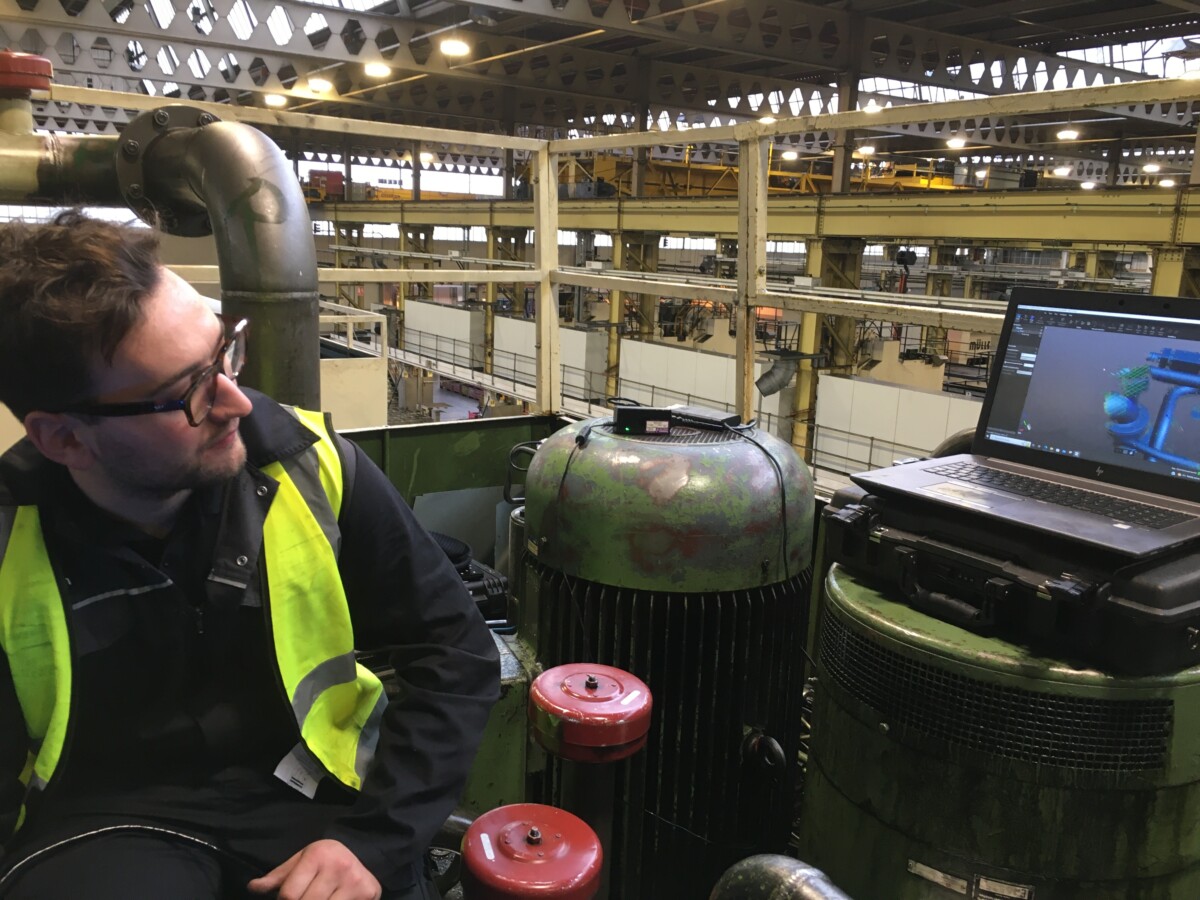
Rotec’s technical team researched and implemented an innovative method to complete replacement tube pipework whilst keeping downtime to a minimum at a large car manufacturing plant in Gloucestershire.
Following damage occurrence on one of their press lines, the world-leading manufacturer required replacement Ø75×12.5 carbon steel tubes.
Traditionally, engineers would be required to remove the damaged tube in order to gather accurate measurements before being able to provide and fit replacements. The removal and installation processes would require manufacturer to shut down the machine during these times.
Downtime for a large manufacturer in the automotive industry can have huge implications operationally and financially. Always keeping the customer at the forefront of projects, Rotec’s technical team suggested using a 3D laser scanner to measure the pipework, in order to minimise downtime.
The 3D laser scanner not only meant that the machine no longer had to be turned off, but the measurements collected were incredibly accurate and minimised the influence of human error. Furthermore, the time required for Rotec engineers to be onsite removing pipes and then measuring them would be dramatically reduced – saving the customer costs due to reduced labour costs.
Once measured accurately, the design for new tubes created using CAD design software in-house at Rotec. In total, the measuring and design process was complete within 2 days.
Continuing Rotec’s commitment to utilising technologies, the tube ends were formed using the Parker HPF system, which eliminates the need for welding of the tube. Bespoke flanges were also machined to suit the formed profile of the Ø75mm tube and accommodate the bolt pattern of the existing connections.
For more information visit www.rotec.net.
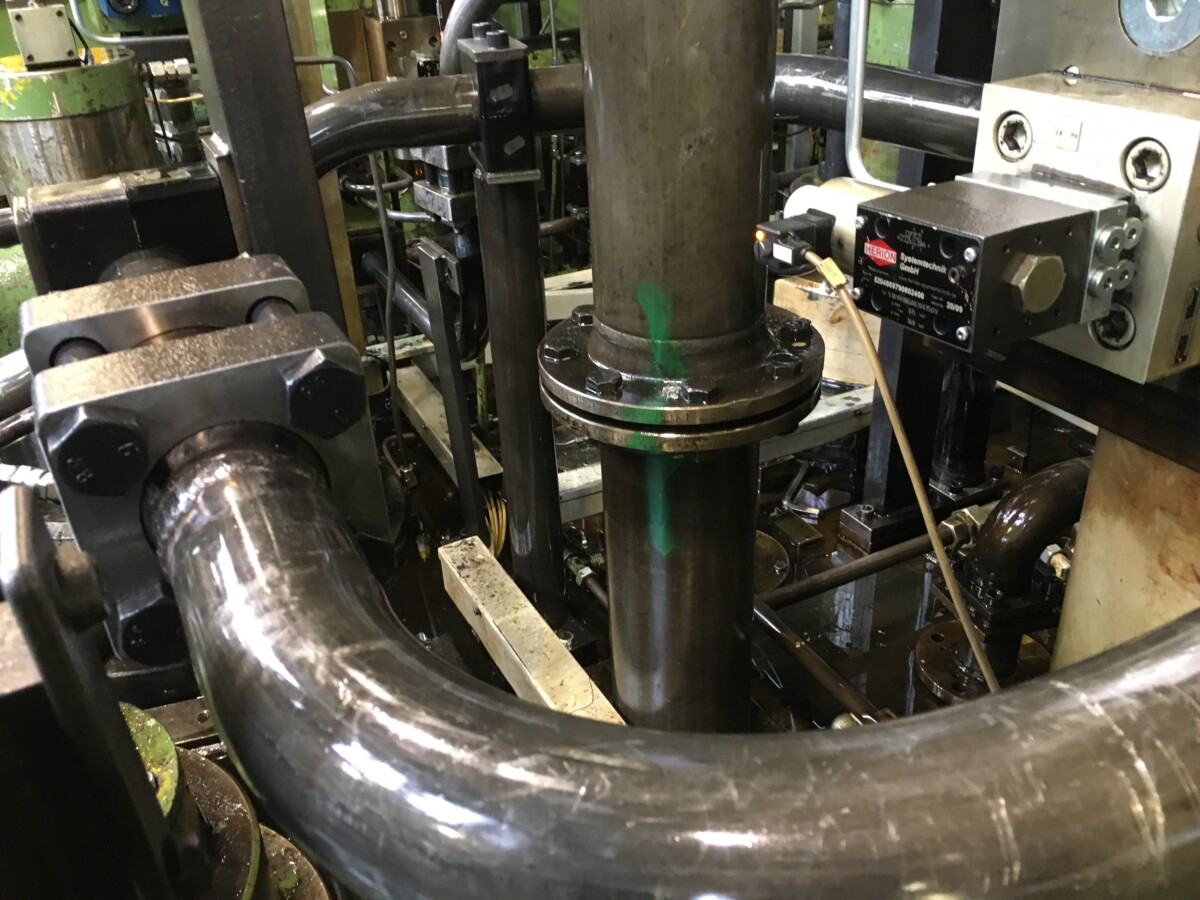
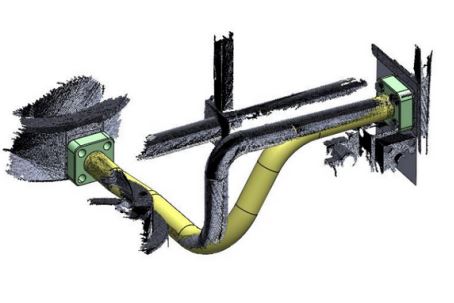