How Rotec Hydraulics Builds Smarter Systems with Parker IQAN Software
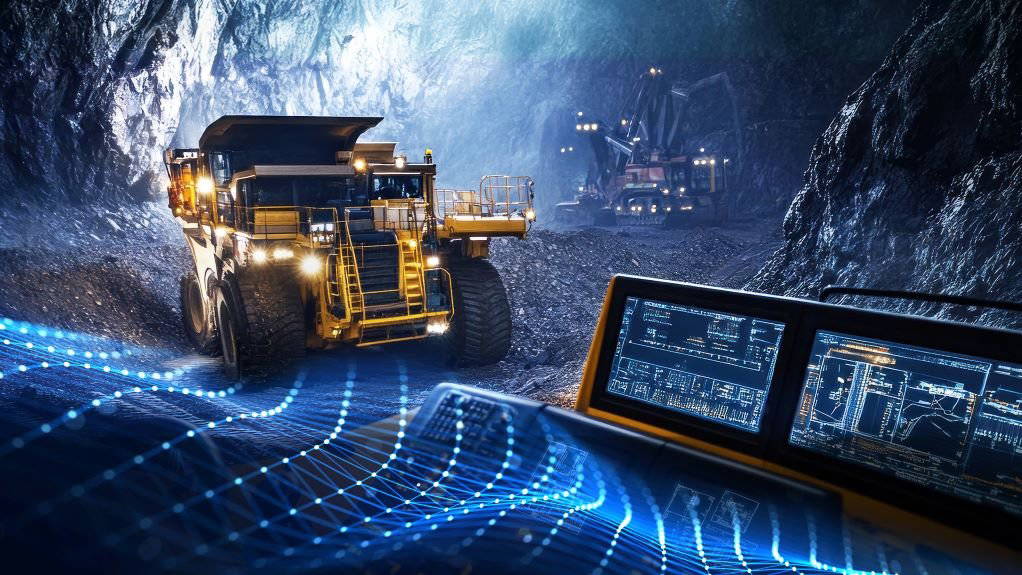
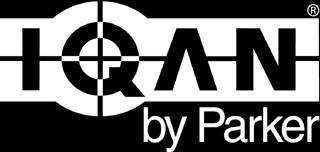
As a certified Parker distributor, Rotec Hydraulics is at the forefront of designing and building custom hydraulic systems that are not just powerful, but also smart. By integrating Parker’s IQAN electronic control system, we create solutions that enhance safety, boost efficiency, and provide unprecedented control over your equipment.
What is Parker IQAN and What are the Benefits?
Parker IQAN is a state-of-the-art electronic control system specifically designed for mobile hydraulic applications. It’s an integrated ecosystem of controllers, displays, joysticks, and sensors, all managed by a powerful and user-friendly software suite.
The key benefit of IQAN is its ability to replace complex mechanical and electromechanical systems with a streamlined, totally electronic approach.
Rotec has successfully designed, built, programmed and installed a variety of custom IQAN-enhanced systems. Clients have reported benefits including:
Enhanced Safety
IQAN controllers enable critical safety features like dual-channel fail-safe circuits and emergency stops which can be operated remotely. This enhances safety – keeping operators out of harm’s way, especially in hazardous environments such as quarries or construction sites.
Precision & Control
The software allows for precise, proportional control of hydraulic functions. Instead of simple on/off levers, operators can achieve infinite speed control and finely tune movements with joysticks and other input devices. This leads to more accurate and efficient operations.
Monitoring & Diagnostics
IQAN systems provide real-time monitoring and advanced diagnostics. The software logs events, and can alert operators to potential issues before they cause a breakdown. This proactive approach to maintenance dramatically reduces downtime and lowers repair costs.
Remote Accessibility
Rotec can build systems that allow for remote monitoring, diagnostics, and even software updates. This means operators can access the system’s data from a laptop or smartphone, diagnose a problem, and potentially resolve it without needing to be on-site.
Customisation
IQAN software is flexible and user-programmable. Rotec Hydraulics’ in-house design team can customize the system to your specific needs, building in tailored functions, adjusting parameters, and creating a user interface on the display that is intuitive for your operators.
Why Choose Rotec?
By choosing Rotec Hydraulics, you’re not just getting a hydraulic system; you’re getting a complete, integrated solution. Our expertise in both hydraulic and electrical mechanical systems, combined with the power of Parker IQAN, allows us to:
- Design and Build: Create bespoke hydraulic power units and control systems from the ground up, tailored to your application.
- Install and Integrate: Seamlessly integrate new electronic controls with your existing machinery, replacing outdated components with modern, smart technology.
- Provide Ongoing Support: Offer remote diagnostics, software updates, and expert maintenance to ensure your system continues to run at peak performance.
Examples of Rotec-designed IQAN systems include a remote control system built for a quarry, which enabled operators to control heavy machinery from a safe distance, drastically improving safety and efficiency. Another project involved the development of a pioneering electric winch system, where Parker IQAN technology was instrumental in achieving precise proportional speed control – a function previously thought impossible for an electric system.
For more information, request a discussion with a member of our Sales Team via sales@rotec.net.