Hydraulic fuel system with integrated pipework solutions carried out by Rotec
Rotec engineers have carried out integration and commissioning of a hydraulic fuel system with pipework solutions on a brand new vessel for a prestigious boatbuilder.
After being let down by another supplier, the client requested Rotec to carry out the works following referrals made by others within the Marine industry who had given Rotec glowing reviews.
A reliable and efficient hydraulic fuel system, built with quality components, aids any vessel engine to run smoothly, avoid unexpected engine failures and ensure passenger safety. Additionally, built and maintained to a high standard, a hydraulic fuel system will be compliant with good practice and environmental regulations.
Rotec’s engineers, whose skills and experience span across multiple engineering disciplines – from hydraulics to electrical – installed and commissioned the hydraulic fuel system in line with the boatbuilder’s schedule of works.
The hydraulic tank design supports 2 hydraulic pumps, driven by 2 engines. The flow rate from each pump (45cc per rev) is estimated at a max 70LPM. The system also supports 2 thrusters, coolers and LS lines.
All pipework solutions used 50mm and 25mm stainless tube with 1.5mm wall thickness. This reduced the number of joints, whilst providing good circulation. Pipework materials centring on the use of rigid tube within the engine machinery space and completion of service points with flexible were employed where required. Finally, pipework was cleaned utilising the pelleting system and flushed.
All hoses were supplied by Rotec and supported by the Parker Tracking System (PTS). This labelling scheme enables a user to quickly scan any asset using a non-subscription, free mobile app. The asset’s technical specifications, including part number are then displayed, enabling efficient and accurate re-ordering of parts when required. App users can also set up service alerts to notify them of when a part’s lifespan is coming to an end.
For more information regarding Rotec’s capabilities, visit www.rotec.net.
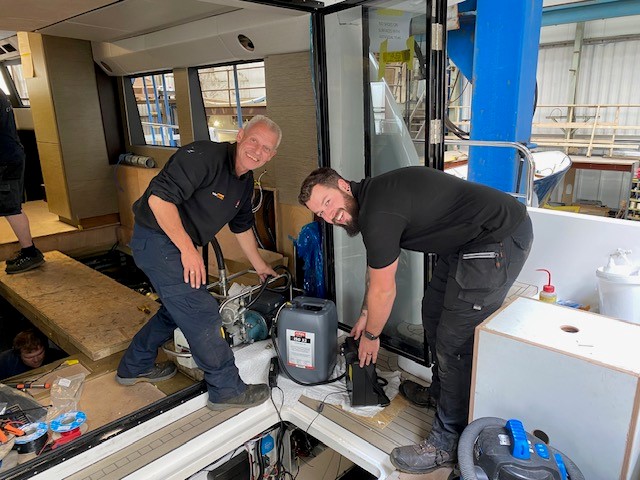
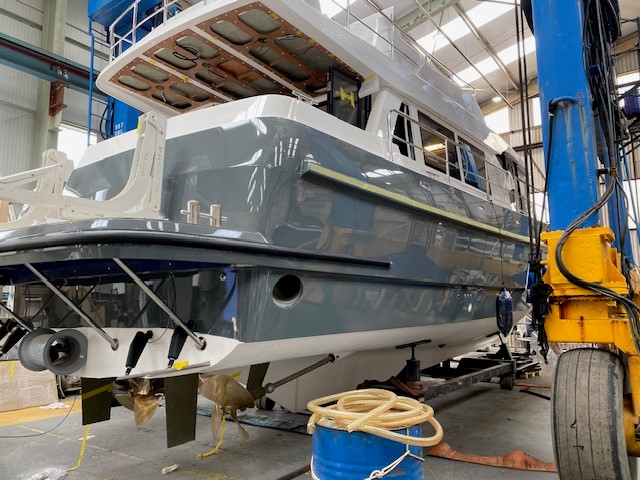