The debate about university degrees versus apprenticeship is nothing new. The truth is there is no direct competition between university degrees and apprenticeships once they get past the application stage. It is like comparing red and white wine – neither is superior, it simply depends on the circumstance and personal preference.
However that doesn’t change the fact that there is a large number of new school leavers each year who are deciding to take the life altering step towards one or the other. Whether this is you or your child / sibling / friend or family member, it is important to know the pros and the cons of each choice as often the school leaver’s talents could be applied to both: apprenticeship or a degree.
Apprenticeships summary
- Generally more hands on work
- Provides in depth training in highly specialised fields
- Earning while studying
- Avoiding student finance and future debt
- Smaller groups in class – more individual attention
University degrees summary
- Highly focused on academic work
- Keeping your career options open with a broader area of study
- Many employers won’t consider applicants with the right working experience if they don’t also hold a university degree
- Lesser barriers to further advancement in the long term
Studying at university offers the option to focus fully on studying for 3 (or more) years and offers a greater diversity of employment options after graduation, which comes in handy if you’re not entirely sure which career path to follow.
For many employers a university degree is also a mark of drive and achievement they find crucial when looking for new recruits.
KIRK KINSELL, European president of InterContinental Hotels says:
“University acts as a filter for people who can prove themselves to have goals, objectives and accomplishments and have survived in that environment.”
There is no doubt that the increase in university fees plays a crucial role when it comes to making a decision. A year after the rise in tuition fees, PricewaterhouseCoopers experienced a 200 % increase in applications for education/working schemes following A levels (comparison of years 2008 and 2011).
However the statistic increase of people not going to university will mean less competition for positions requiring degrees in the long term.
Kirk Kinsell says “If we think about today versus 20 years ago, today’s companies put a lot more emphasis on degreed candidates. I think degrees will be even more important in 20 years’ time.”
And it is likely this trend will indeed continue; a report recently launched by Boris Johnson claims that by 2022, 60% of jobs in London will be at degree level. This would suggest that apprentice trained workers will struggle reaching for high level jobs and will likely be eventually pressured into further education.
This being said, there is a probability that any further education will be paid for by an employer, leaving the formal apprentices virtually debt free, which is undeniably a rare occurrence in the current financial climate and may contribute towards overall life satisfaction factor.
There has been a long prevailing misconception in relation to apprenticeships best voiced by Steve Holiday, the Chief executive of National Grid:
“What we’re in danger of moving towards is an attitude of ‘if you go to university, you’ll be successful or if you’re not quite as successful, you go down these alternative paths’ “
The sentiment is clearly outdated if not wrong altogether. There is a demand for educated graduates, but there is also a huge need for highly skilled technicians. Many apprenticeship positions are as prestigious as a spot at the top 10 university:
“From receiving 9,000 applications in the year starting August 2009, BT received 33,000 for the following 12-month period for 500 places. In the same year, Oxford University received 17,000 applications for 3,000 places. BT is looking to broaden the scope of its scheme to include more IT roles and may take on up to 250 additional apprentices this year.”
(ANDY PALMER, Head of skills, BT)
People who opt in to enrol on in house training schemes or apprenticeship schemes have often progressed into senior roles within the company.
IAN POWELL, Chairman of PricewaterhouseCoopers says:
“Students joining the firm on this route earn a competitive salary while studying for a professional qualification, plus there are no student debts to repay. One of our current board members joined the firm as a school-leaver and is a great example of the fact that those who don’t pursue a degree can make it to the top of the firm.”
Whether you decide to go to university, join an apprenticeship or an in-house training scheme, it is, without a shadow of a doubt, worth considering a career in engineering.
(What is it like to be a Woman in Engineering? We asked Claire, our electrical engineer)
The engineering industry in particular has been struggling with a shortage of talent, the problem being more a case of quantity rather than quality however. The companies agree that the individuals recruited are excellent, willing to learn the skills necessary and learning fast. The situation seems to be worse for smaller business, with smaller marketing and recruitment budgets, it is difficult for them to get themselves in front of school leavers and graduates at first place. So what happens then is that a large number of applicants compete for a small number of jobs with the industry giants, and often get discouraged if unsuccessful, finding jobs in other industries, while small companies (especially the ones in more remote areas) are screaming out for suitable candidates.
Rhys Morgan, director of engineering and education at the Royal Academy of Engineering says:
“However, even if all these issues were addressed and 100 per cent of engineering graduates went into industry (a questionable aim in itself), we still wouldn’t have addressed the skills shortage we’re told companies are facing. In short, we need more engineering students. And this can’t be addressed just by engaging more with young people’, said Morgan. ‘Universities are almost at capacity,’ he said. ‘So even if we did get more students coming through to study STEM [science, technology, engineering and maths] subjects, we’re not going to have the capacity. There’s a real timebomb coming up.’
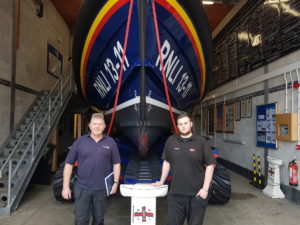
Apprentice Zac Huckle with his mentor
This is why companies like Rotec offer apprenticeships or in house training schemes.
(See interview with Zac Huckle, our engineering apprentice)
For anyone considering an engineering career and would like to find out more
about the options available to them please follow:
http://www.tteltd.co.uk/engineering-apprenticeships-or-university/
If you would like to search for specific apprenticeships and study courses you can look here:
http://www.tomorrowsengineers.org.uk/apprenticeships/
http://www.notgoingtouni.co.uk/sector/engineering
Sources:
https://www.theguardian.com/money/2011/may/15/graduate-jobs-university-work-experience-apprenticeships
https://www.theengineer.co.uk/issues/april-2014-online/why-are-engineering-firms-struggling-to-recruit-graduates/
http://www.tteltd.co.uk/engineering-apprenticeships-or-university/
http://www.tomorrowsengineers.org.uk/apprenticeships/
http://www.bbc.co.uk/news/education-33254142