Streamline Your Manufacturing with Rotec’s OEM Kitting Service
In today’s competitive manufacturing landscape, efficiency and cost-effectiveness are paramount. Original Equipment Manufacturers (OEMs) are constantly seeking ways to optimise their operations, reduce lead times, and improve productivity. One solution is Rotec’s bespoke kitting service -streamlining your assembly lines and reducing lead times, it helps improve your time-to-market and gain a competitive advantage.
What is an OEM Kitting Service?
OEM kitting involves assembling all the necessary components for a specific product or sub-assembly into a single, convenient kit. This can include everything from hose assemblies, adaptors, seals, and o-rings, to pumps, valves, oils, and filters – essentially, any component your product requires. Rotec Hydraulics works closely with OEMs to tailor these kits to their exact specifications, ensuring every part is present and accounted for.
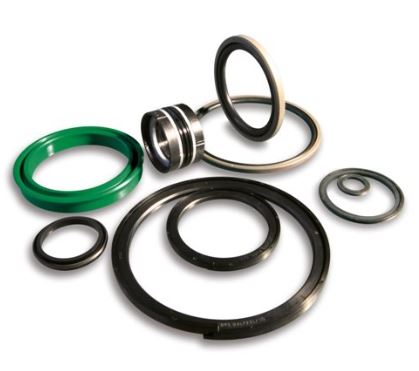
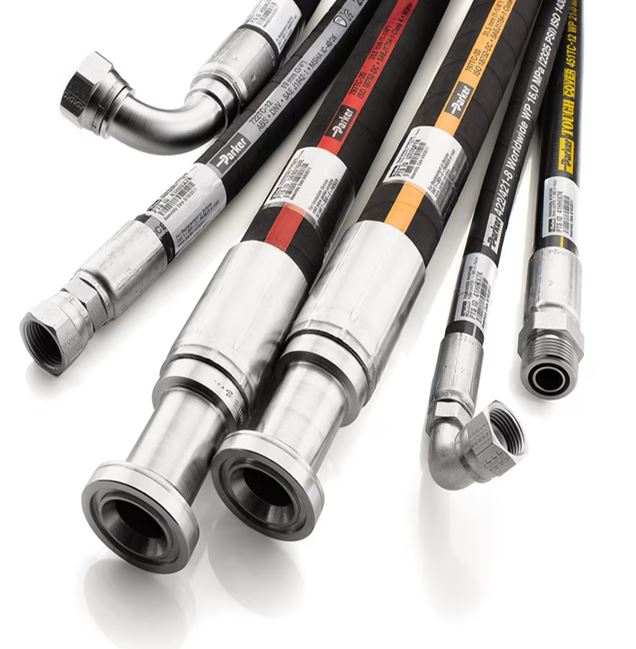
How Rotec’s Kitting Service Benefits Your Business:
Our OEM kitting service is designed to be a complete solution, offering a range of value-added services, including:
- Customized Kitting: We work with you to understand your specific needs and create kits that perfectly match your requirements. No more searching for individual parts – everything you need arrives in one package.
- Comprehensive Component Sourcing: We handle the procurement of all necessary components, saving you time and effort. Our extensive network of suppliers ensures access to high-quality parts at competitive prices.
- Value-Added Services: We can include testing, labeling, bagging, and other services to further streamline your production process. Just let us know your requirements, and we’ll take care of the rest.
- UK and European Coverage: Rotec Hydraulics serves clients across the UK and mainland Europe, ensuring consistent supply regardless of your location.
- Reduced Costs and Improved Efficiency: Kitting can significantly reduce your purchasing activity, speed up goods receipt, and improve productivity. By consolidating your supply chain, you can also reduce the number of suppliers you need to manage, leading to fewer invoices and simplified administration.
“Rotec’s kitting service has streamlined our assembly lines, reducing assembly time and boosting productivity.”
Partner with Rotec Hydraulics:
If you’re looking for a way to optimise your manufacturing processes and improve your bottom line, consider partnering with Rotec Hydraulics for your OEM kitting needs.
Contact us today to discuss your requirements and discover how we can help you achieve your goals. Let us help you build a more efficient and competitive business.