Rotec Celebrate as Double Finalists at the Somerset Business Awards 2022
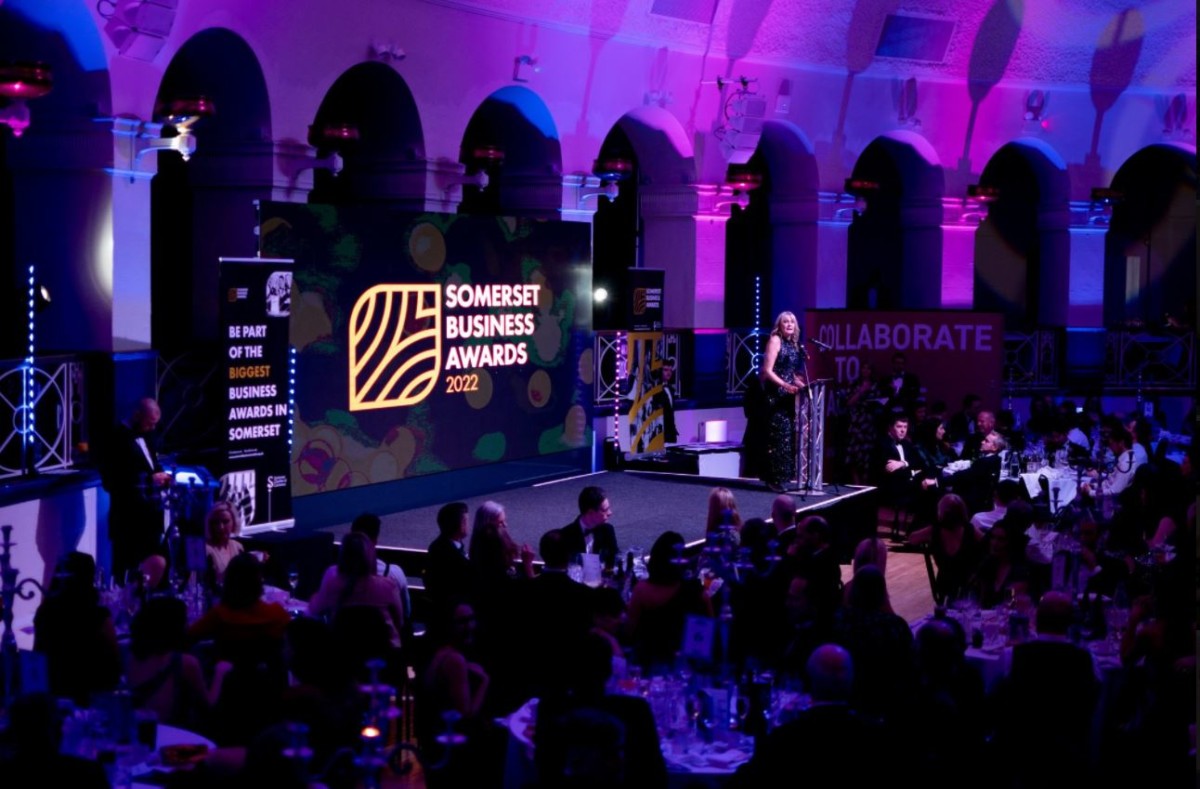
Rotec Hydraulics Ltd celebrates being double finalists at this year’s prestigious Somerset Business Awards (SBAs) for ‘Best Use of Technology’ and ‘Somerset Manufacturer and Producer’ Award.
The awards, run annually by the Somerset Chamber of Commerce, received a record- breaking number of entries and only the most outstanding businesses with a head office in Somerset were named finalists.
Our investment and integration of Parker Internet of Things (IoT) technology earned us a place at the grand final in the ‘Best Use of Technology’ award category. IoT enables engineers to remotely control and monitor various performance and safety parameters using strategically placed, wireless sensors to provide data and control systems over the internet.
Named finalist for the ‘Somerset Manufacturer and Producer of the year’ category is testament to the team’s innovative development of several bespoke winch systems for both leading regional and national names within the Utilities sector.
Somerset Chamber Executive Director, Emma Rawlings, said,
“These awards are the largest in Somerset and are a fantastic opportunity to celebrate all that
is great about [Somerset’s] diverse business community.”
Paul Prouse, Managing Director, commented,
“Being named finalist in two categories is a testament to our team who have continued to provide solutions and outstanding products and services to our customers throughout a challenging period for all businesses.
“Investing in and utilising cutting-edge technologies and providing innovative solutions for our clients has always been at the heart of our business.”
The winners were announced at the Grand Final on 11th March, which celebrated the extraordinary organisations within the county of Somerset. Rotec finished as double finalists – a great achievement amongst such a high calibre of local businesses.
Pictured below (left to right): Roger Carne, Paul Prouse, Rachel Worth, Richard Lang, Mark Conniff, Josie Chamberlain, Richard Renfree and Andy Rimes.
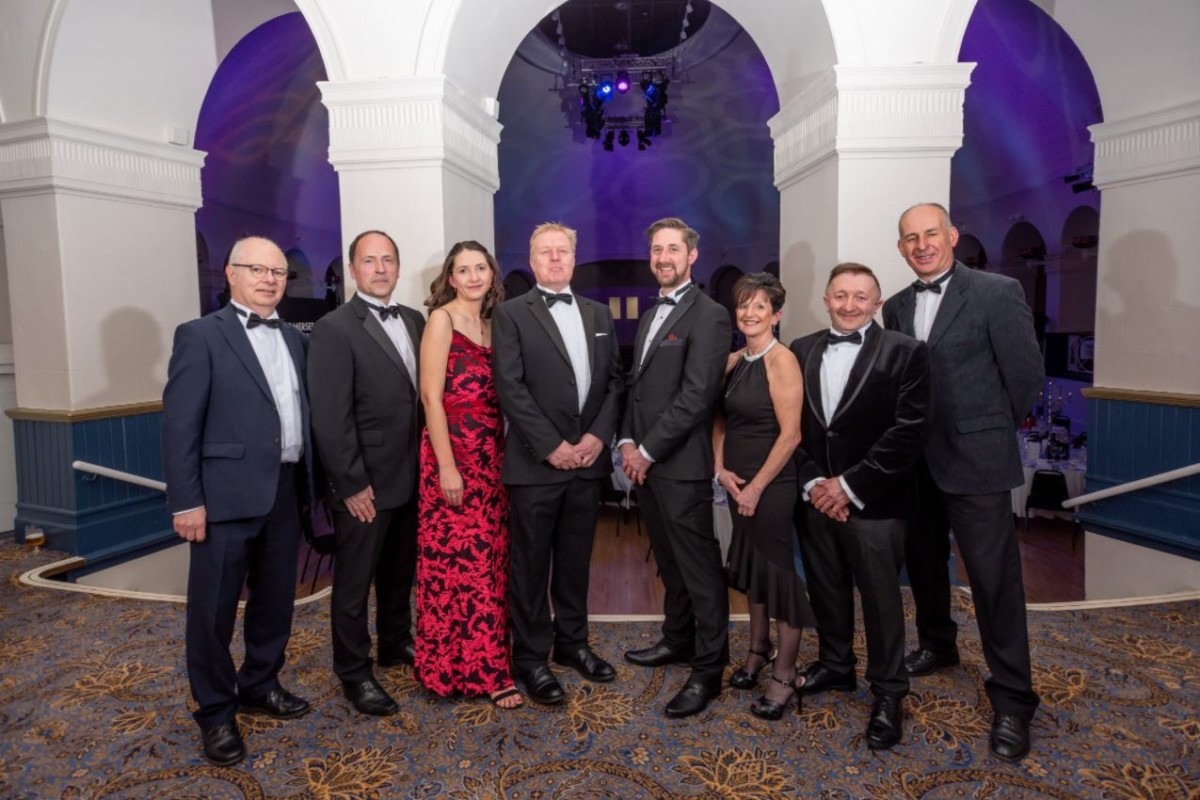