Hydraulic Accumulator Overhaul & Recertification for UK Port
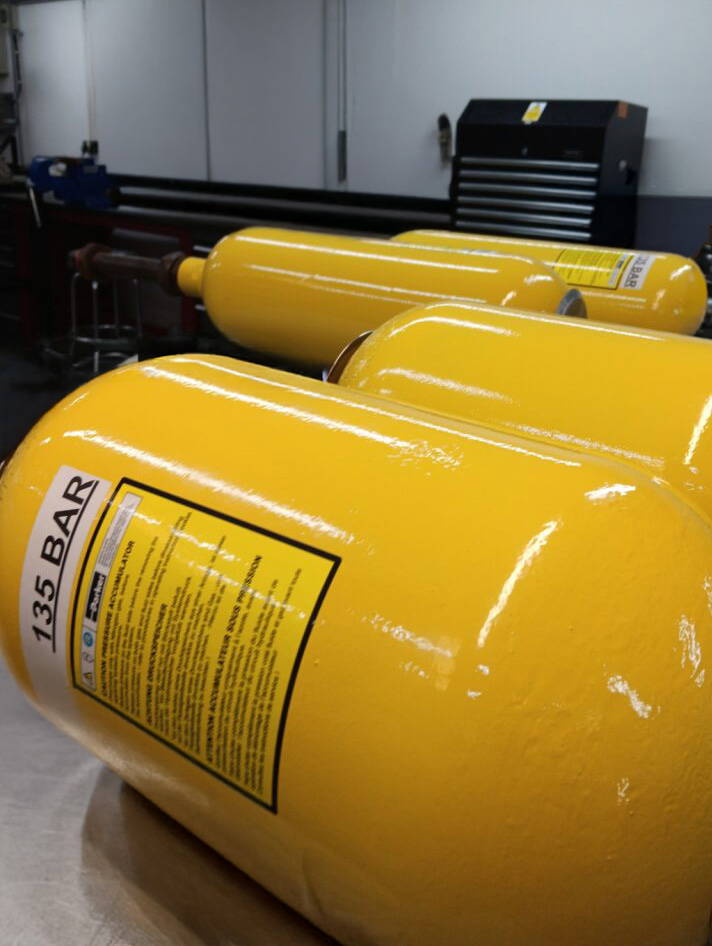
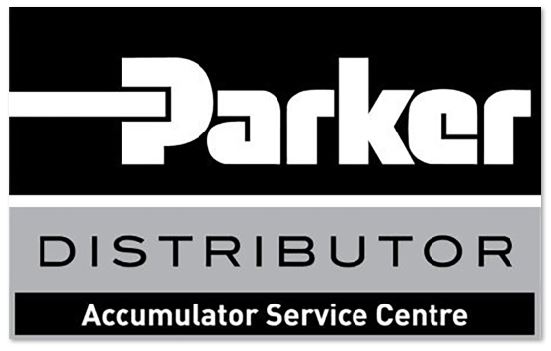
The Challenge:
Our client – a major UK port offering shipping, logistics, and cargo handling services for industries worldwide – needed a critical service for their 10-litre and 20-litre, 135 bar hydraulic accumulators. These components, vital for port machinery, operate in a harsh, submerged saltwater environment, which had led to significant corrosion and wear. The accumulators required a full overhaul and recertification to ensure safety and continued operation.
Our Solution:
The Rotec Hydraulics team performed a comprehensive service to restore the accumulators to a like-new condition.
- Full Overhaul: We disassembled the units, replaced all internal bladders and seals, and prepared the shells for a new protective coating.
- Corrosion Treatment: To combat the effects of saltwater, we shotblasted the accumulators to remove all rust and old paint, creating a clean surface.
- Protective Coating: We applied a durable, high-performance marine-grade paint system designed to withstand the harsh conditions of their working environment.
- Recertification: Finally, each accumulator was recertified through rigorous pressure and leak testing, ensuring they met all safety standards and operational requirements.
The Result:
The accumulators were returned to the customer fully overhauled, recertified, and protected against future corrosion. Our work extended the lifespan of these critical assets, minimizing downtime and ensuring the continued reliability of their port operations.
Rotec Hydraulics are the only certified Parker Hannifin Accumulator Recertification Centre in the South West of the UK – servicing and re-certifying accumulators of all brands.
For reliable hydraulic solutions in challenging environments, contact Rotec Hydraulics via 01823 348900 or email sales@rotec.net.