Rotec achieves Parker Certified Accumulator Service Centre recertification
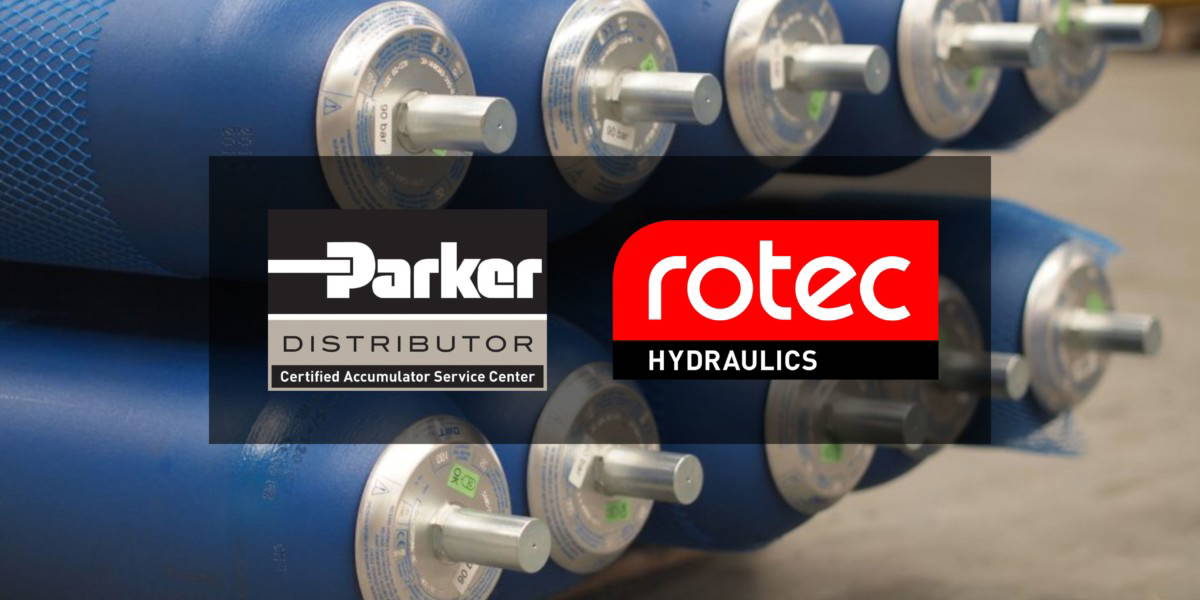
Rotec is pleased to announce it has been re-certified as a Parker Hannifin Hydraulic Accumulator Service and Technology Centre.
Following successful completion of an audit process for Hydraulic Accumulator Technology and Service Centres, Rotec Hydraulics Ltd has retained its prestige as the only certified Parker Accumulator Service and Technology Centre in the South of the UK.
Parker Certified Accumulator Service Centres were established to enable the combination of industry-leading products with excellent customer service, and to deliver stress-free accumulator management with maximised performance, efficiency, and safety.
The benefits of being a Parker certified centre, in addition to Rotec’s status as a Parker Hydraulic Technology Centre, enables Rotec Hydraulics to provide integrated solutions that combine products, services and technologies. Rotec’s access to original spare parts provides tangible benefits to clients, including shorter inspection time and the reduction of complexity help to lower cost and to save time.
As added value to customers, the Rotec Hydraulics Ltd Service Centre is able to utilise the Parker Tracking System (PTS) which helps schedule accumulator maintenance, providing automated notifications on inspections and replacement parts.
Rotec Hydraulics have the knowledge, expertise and capabilities to deliver a comprehensive range of accumulator services including:
Regulatory compliance and certification
- Hydraulic accumulator re-certification
- Provision of tracking systems, data monitoring and recording
- Optimising customer documentation to fulfil regulatory requirements
- Local pressure vessel regulation
- Audits, scheduled inspections and replacement parts
Hydraulic accumulator maintenance and pre-charging
- Full service for just in time solutions and breakdown repairs
- Full service for replacement and planned/preventative maintenance
- Commissioning/testing (on-site)
- Bladder and piston seal replacement
- Gas pre-charge control and re-charge
System Optimisation
- System design and improvement (including Hydraulic Power Units (HPUs) and Accumulator Racks, calculation, training and measurement)
- Accumulator replacement
Asset Management
- Energy and efficiency audits
- Risk assessment and servicing of safety equipment
- Asset condition monitoring and prognostics (sensors)
- Legal conformity and insurance cover
- Enabling customers to exploit the potential of Condition Monitoring and the use of Internet of Things (IoT) technology.
For more information on Rotec’s ramge of Accumulator services, contact our team.