Choosing the correct hydraulic filter
Filtration is undeniably one of the most important components in any hydraulic system. Choosing the correct hydraulic filter can increase a machine’s life expectancy and lower the risk of expensive component damage.
Establishing the Target Cleanliness Level
We recommend identifying the most sensitive component in your system and learn the filtration cleanliness level (or micron rating) for that component. This is often a variable piston pump or the proportional valve. By using a recommended cleanliness code chart, you can determine the ISO code for a range of the most critical components such as pumps, valves, actuators, and more. From this ISO code, you can select the appropriate filter from your preferred manufacturer’s catalogue. Contact our team if you are unsure.
Achieving Target Cleanliness
There are generally four major factors in positioning contamination control devices in a hydraulic or lubrication system to achieve the target cleanliness level that is required.
Initial filter element efficiency
Filter element efficiency under system stress
Location and sizing of contamination control devices in the system
Filter element service life of the system
While all of these factors are important, filter manufacturers (such as Parker, Eaton and MP Filters) typically design their filters for maximum efficiency, so you have more responsibility to ensure the location and filter sizing is correct to increase the longevity and reduce maintenance damage to your hydraulic system. When done correctly, this will give the best service life of a system.
Selecting The Right Filter Type
Suction filters are usually put in a tank to filter out any large items, such as bolts or rags that may have dropped in the reservoir. They are not generally used for filtering your fluid to the required ISO code.
Pressure filters come highly recommended because they are placed after your pump, so if the pump was to fail, all of the components downstream would still be protected. These filters must be rated for your system’s running pressure and ISO code.
Return filters are important because they clean the oil before it returns to your hydraulic reservoir and therefore keep your reservoir clean and free from dirt particles. Return line filters are generally used in open-loop applications and should be rated at the ISO code that your system requires.
While all three filter types are generally not needed in the same system, it is important to have at least one pressure filter or one return line filter in every application to maintain the fluid cleanliness level that hydraulic components require.
Selecting The Right Filter Size
Once you determine what type of filter to use, you must consider the pressure drop through the filter. In most cases, pressure filters and return filters have a bypass that protects the system when the filter gets clogged or plugged. It allows the oil to go around the filter element and allows the system to run even though it’s not being filtered. Do keep in mind that your system would be running unfiltered with this setup.
As your filter becomes dirtier, it requires more pressure to push the oil through the element because it is clogged with dirt and debris. Once the pressure required reaches a certain point it becomes inefficient and starts wasting horsepower in the hydraulic system; this is the reason for the bypass. Typically, bypass settings on pressure filters are 40-50 PSI to limit this inefficiency.
When sizing a pressure filter, generally we would like to keep the pressure drop through the filter under 10 PSI. This gives your filter more time to get to the 50 PSI bypass setting, thus increasing the length of time between element changes. If you size your filter with a 25 PSI pressure drop you are already at half of your filter life (assuming 50 PSI bypass). If we selected a filter that only had a 10 PSI pressure drop, your filter will have 40 PSI of pressure drop before it reaches bypass setting, thus, allowing the element to last longer before needing service or be replaced.
Another consideration is oil viscosity. Thicker oil will cause a higher pressure drop, so you need to know what oil you are going to run in your system to truly size the filter correctly and get the best filter life for your application.
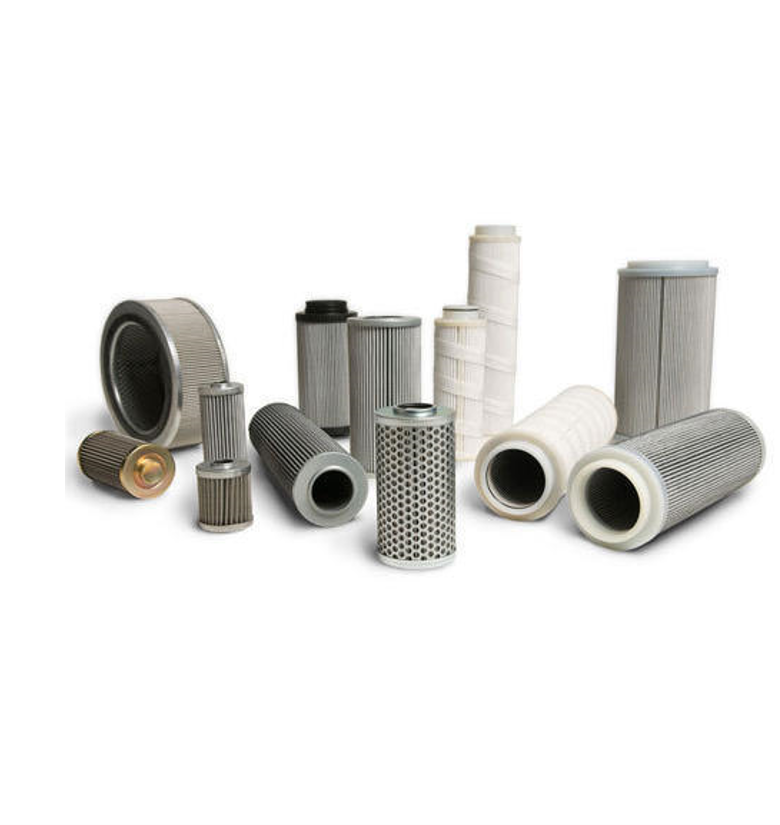
Effects Of Hydraulic Oil
Choosing the correct filter is only part of the equation. New hydraulic oil straight from the drum has a typical cleanliness level of ISO 4406 23/21/18. From what we learned above you can see that this is 16-64x dirtier than what most hydraulic systems require (each single number increase in the ISO code is double the contaminant level for that micron size)! To put it another way, a 25 GPM pump operating continuously in hydraulic oil at 23/21/18 will circulate 3,500 pounds of dirt to the hydraulic system’s components each year.
Extend Filter Life By Using Clean Hydraulic Oil
To add hydraulic oil, and not the dirt, always filter new oil prior to use in a hydraulic system. This can be done in a number of ways. The most common way is to use a filtration cart or kidney loop filter in your reservoir. Schroeder makes an exceptional filter cart that can not only remove dirt particulates from new oil, but also water, if needed. Carts like these offer great value for your investment, as they range from relatively low cost to expensive, depending on what you are trying to accomplish. Also, if you are already running Schroeder mobile filtration on your machine, then there is a good chance you can use the same filter element that you already use, thus reducing inventory parts.
Another way to pre-filter your hydraulic oil is by pumping the oil into the hydraulic reservoir through the system’s return filter. The easiest way to do this is to install a tee in the return line and attach a quick-connector to the branch of this tee. Attach the other half of the quick-connector to the discharge hose of a drum pump. When hydraulic oil needs to be added to the reservoir, the drum pump is coupled to the return line and the oil is pumped into the reservoir through the return filter. Benefits of this method include reduced spills and prevention of ingress of external contamination.
While many people don’t even think about filtering new oil, it is very important to get clean oil into the system. It is much easier to prevent dirt from getting into a system by using precautionary measures than it is to remove dirt from a hydraulic system. Once the dirt ingresses, it is very difficult to get the system clean.
When To Change Hydraulic Fluid
Maintaining the hydraulic fluid in your machine is an important consideration when choosing and extending the life of hydraulic filters. It’s challenging to set an expiration on hydraulic fluid introduced into your system, even under ideal circumstances. Over time even well maintained oil will wear out, however here are a few factors that affect hydraulic fluid and when filter changes are more than likely necessary.
Contamination
Contamination, in the context of having to change your hydraulic fluid, means you have debris in the fluid than the filtration system can reasonably remove. This is usually some sort of particulate contamination event that overruns the system’s onboard filtration. This can also include contaminating situations such as getting water mixed into the fluid (looks cloudy) or mistakenly topping off your hydraulic reservoir with the wrong fluid. It may be possible to salvage your particulate or water contamination situation using some sort of off-line filtration asset.
Heat
This one is simple. If you get your fluid gets too hot, it breaks down. Most of the time you know it got too hot because it becomes darker in color and it doesn’t smell right. It usually doesn’t take the time and expense of a fluid sample analysis to figure this one out. Heat accelerates the condition called oxidative degradation.
Oxidative Degradation and Additive Depletion
This one is a little more complex and will require a fluid analysis to determine. By performing routine fluid analysis a degradation or depletion trend can be spotted before it becomes a mechanical maintenance event.
A hydraulic oil’s oxidative degradation is determined by its Total Acid Number or TAN. As the name implies, this is the absolute measure of the total acid number in the fluid. Over time, oxygen will combine with the hydrocarbon molecules of the oil and a chain reaction occurs. This action results in some obvious conditions like darkened oil, varnishing, and sludge. Some conditions that are not so obvious are increased viscosity, increased foaming, and retained air.
A hydraulic oil’s additive depletion is determined by comparing the used oil’s elemental analysis to the baseline of identical new oil. For example, zinc is an antioxidant and anti-wear additive. Over time it gets depleted, so it’s important to check the concentration of zinc in your current oil to the concentration of zinc in the same new oil.
Rotec’s technical experts have many years of experience in applying the right components for maximum effectiveness and overall lower total cost of ownership. They can help you to improve efficiency and save money over the life of your equipment. Contact our team today for help in finding the correct filter and oil for your hydraulic system.