Rotec Delivers Critical Engineering Solutions for Cruise Ship
Rotec, a leading provider of hydraulic, pneumatic, and electro-mechanical solutions, is proud to announce the successful completion of critical engineering works on a cruise ship at Falmouth Dry Dock. This project follows a successful dry-docking of a sister ship the previous year.
The Challenge
We were asked to carry out essential maintenance requirements on the vessel, specifically focusing on the ship’s main engine combustion fans, supply fans, and exhaust fans.
The scope of work was comprehensive, requiring skilled engineering capabilities. Key objectives included:
On-site bearing replacement where feasible.
Thorough inspection and pre-recording of electrical readings before disconnection.
Safe electrical and mechanical disconnection of units.
Post-disconnection inspection and recording of insulation values.
Reporting any abnormal findings to the ship’s staff.
Cleaning of all necessary areas.
Extraction of old bearings and fitting of new, Rotec-supplied bearings.
Reinstatement and electrical/mechanical reconnection, including insulation tests.
Optional services like dynamic balancing and laser alignment were available.
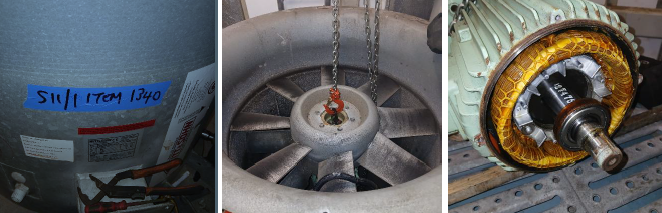
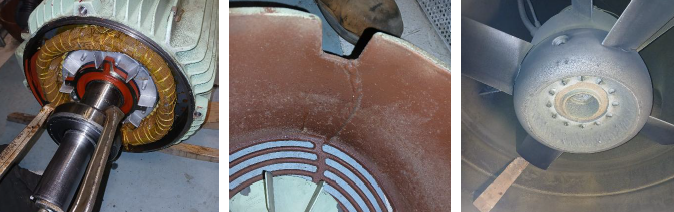
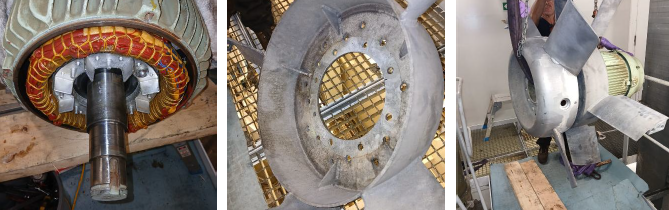
The Solution
Rotec deployed a team of highly skilled engineers to the dock, who quickly commenced work on the specified fan units. Their methodical approach ensured every step was executed with precision and adherence to safety protocols.
During the process, the team identified several critical issues that required immediate attention:
A supply fan, upon removal from its trunking, revealed cracks in its mounting bracket, which were promptly welded for repair.
A significant crack was discovered on the lug of the Non-Destructive Examination (N.D.E) endshield. Rotec swiftly sourced and fitted a replacement endshield, adapting it for the absence of a vibration sensor aperture.
Both vibration sensors for the bearings were found to be damaged beyond repair, necessitating the sourcing of new replacements.
The fan cowl also showed evidence of a previous crack and weld repair.
Despite these unforeseen challenges, Rotec’s engineers demonstrated exceptional problem-solving skills and adaptability. The fan unit was meticulously reassembled with new, high-quality bearings supplied by Rotec. A rigorous insulation test was performed, yielding a reading greater than 2Ω, confirming the unit’s electrical integrity. Following reassembly and testing, the unit was run to the complete satisfaction of the ship’s staff.
The Feedback
The client’s Assistant Electrical Manager commented,
“I’d like to personally thank your engineers for their excellent work. As always, they have been a pleasure to work with, delivering the job on time and to a high standard. All work has now been tested and officially signed off by the ship.”
Conclusion
By proactively identifying and resolving complex issues, Rotec ensures that critical marine equipment functions optimally, contributing to the safety and efficiency of global maritime operations. Our engineers carried out the job within the timeframe required – something that is critical to the Marine industry. Rotec looks forward to continuing its partnerships, and further supporting the marine industry within Cornwall, the South West and beyond.
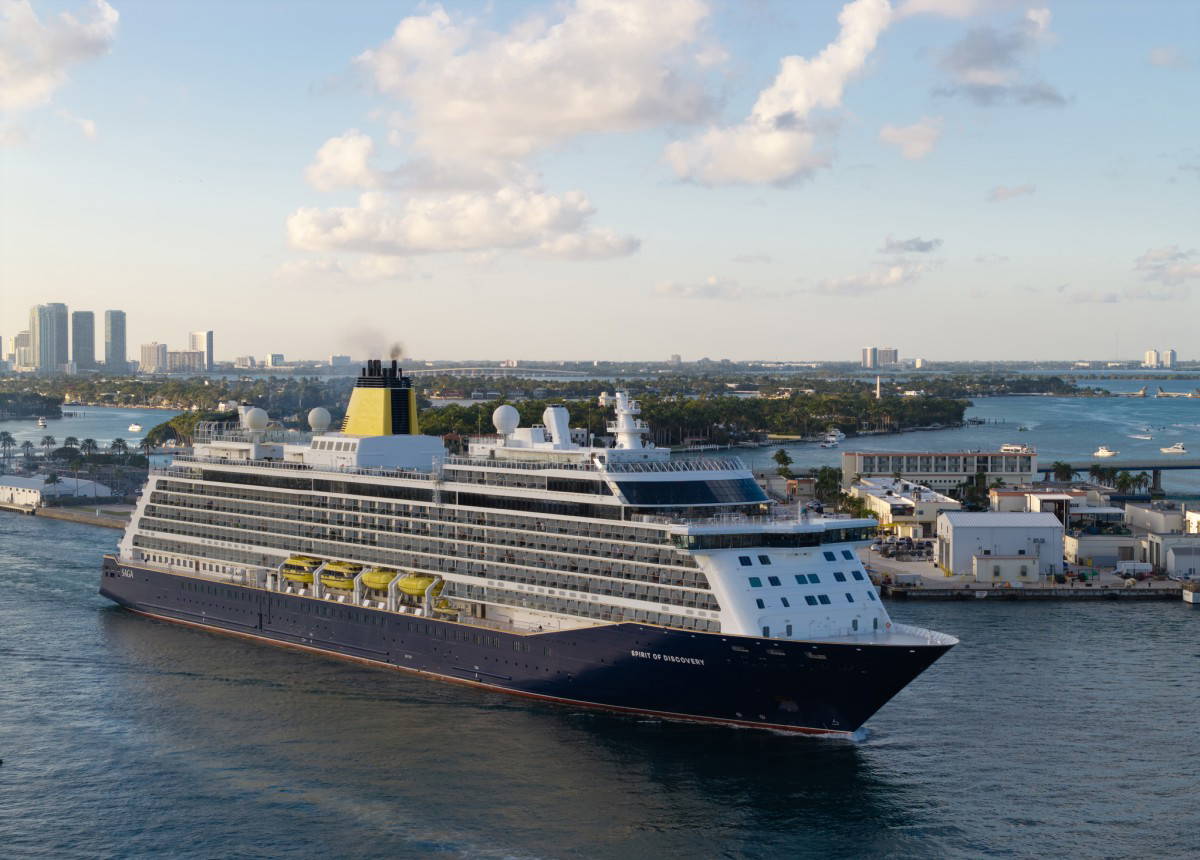