Stroud Engineers Deliver Major Refurbishment Projects at BMW
Rotec engineers carried out a major refurbishment of the Feed Line and Press at a BMW plant in Gloucestershire.
Over 160 hydraulic hoses on the Feed Line, and 66 hoses on the Major Press were removed and new hoses made and fitted.
This was a challenging job due to the complexity of the machinery and included hoses on the Feed Line HPU (hydraulic power unit), Press and Overload/Protection/Lubrication HPUs. Feed Line Pneumatic cylinders, valves and tubings were also supplied and fitted, in addtion to a total of 48 existing hydraulic cylinders on the Feed Line removed and new cylinders fitted.
Further work taken on the Feed Line, Press and Overload/Protection/Lubrication HPUs included:
- Draining of the working fluid and cleaning of the reservoir.
- Replacement of pressure and return hydraulic filters, pressure and return.
- Replacement of pressure and return hydraulic filters, pressure and return.
- Resealing of duplex filter block.
- Removal of existing and refitting of new motor pump sets.
- Thorough cleaning and inspection.
- Removal of existing and refitting of new air blast coolers.
All refurbishment works were carried out on time, in budget and to the client’s expectations and standards.
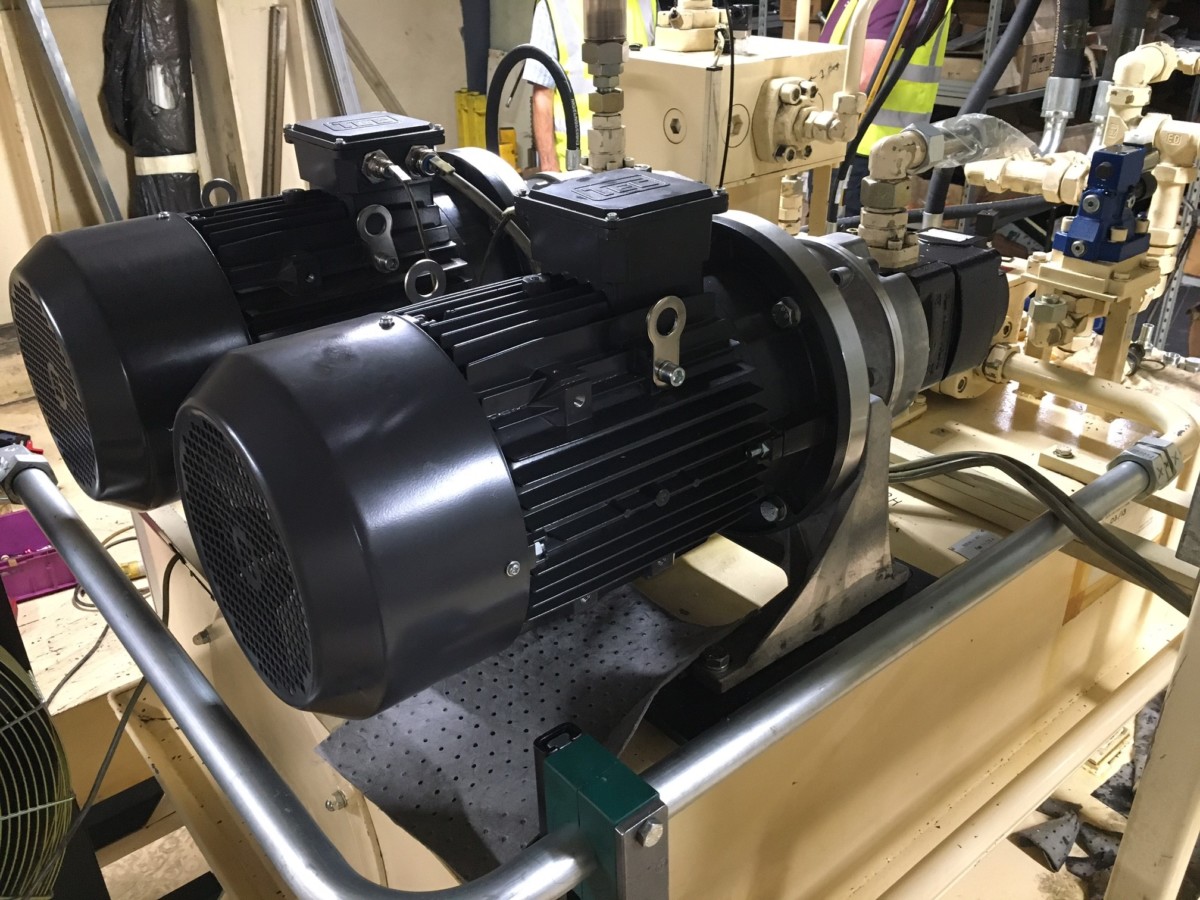