Reports suggest around 80% of all hydraulic failures are thought to be caused by fluid contamination* making regular, effective oil analysis a top priority for any business working with hydraulics.
Hydraulic component contamination is unwanted, foreign matter found within hydraulic fluid. Occasionally contamination is easy to spot. However, most of the time contamination is not visible to the human eye. Regardless of whether the contamination is visible or not, contamination has the potential to severely damage hydraulic components and systems.
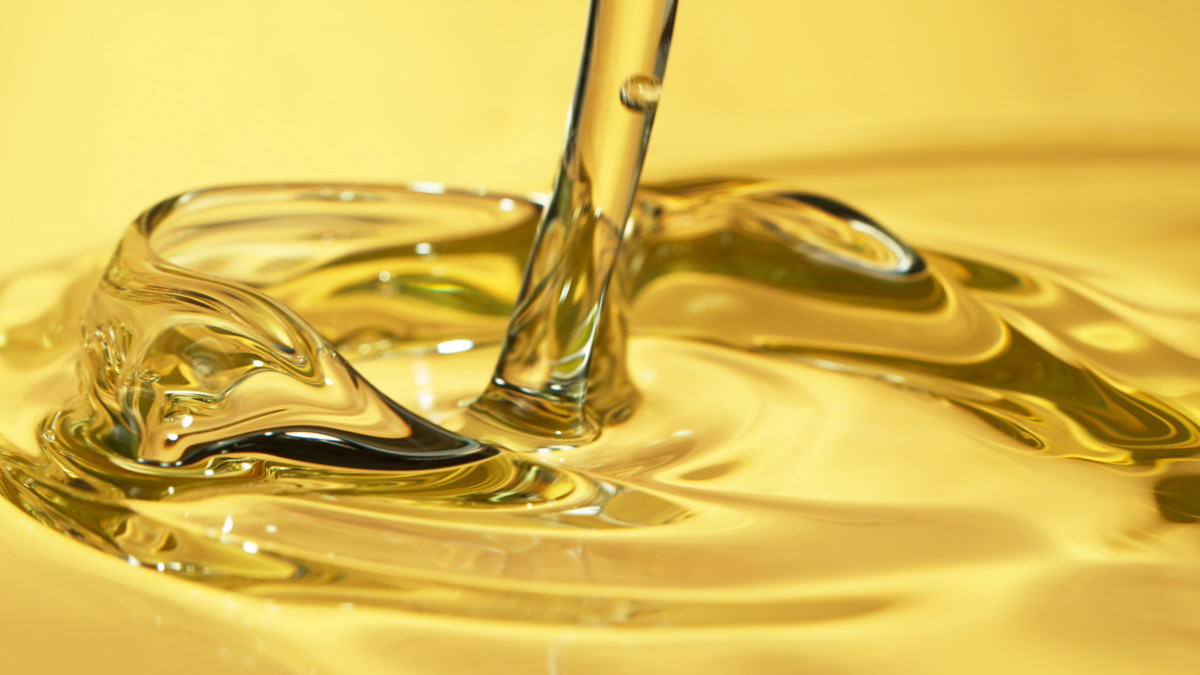
Different types of hydraulic contamination
Contamination may be classified as abrasive or non-abrasive. Abrasive contamination involves particles that enter the hydraulic system, for example small paint flakes falling into the system during routine servicing, or a few grains of core sand left over from casting. Non-abrasive contaminants can be just as damaging and include particles, such as the remnants of shredded elastomeric seals from a pump, or chemicals, such as the by-products resulting from the oxidation of the oil or the result of reactions involving additives. While not abrasive, these contaminants can still have an extremely negative impact on the hydraulic performance of motors and pumps.
Some experts classify hydraulic contamination in three ways: gaseous, liquid or solid. Gaseous contamination negatively alters lubricating properties of a hydraulic system, creating wear and thus increasing the risk of further contamination. Liquid contamination also impacts lubricating capabilities as well as causing rust. Solid contamination can be responsible for valve blockages, substantial pump damage and blown seals and gaskets.
Recognizing the Sources of Fluid Contamination
Brand new fluid can be contaminated. Fluid contamination can occur during the manufacturing of the hydraulic oil, therefore before adding any power fluid to a hydraulic system or component (including reservoirs, pumps, valves or motors) it should be carefully filtered through a fluid servicing cart/unit. Be aware that contamination can also happen when fluid is being transferred or added to a hydraulic system.
Even new equipment and components can be contaminated. Whether it’s a new equipment or components, contamination may already have occurred either during the manufacture or assembly of the product. Smears of grease, tiny particles of weld spatter, or a thread from a rag have all been found to pollute brand new hydraulic systems and components.
During normal operation, some contamination will form. This includes non-abrasive chemical contamination caused by chemical reactions being triggered as the hydraulic fluid ages or is exposed to higher temperatures than originally recommended. Further, abrasive contamination can occur due to physical damage to hydraulic components, such as the rotating group in a hydraulic motor or failed bearings in a hydraulic pump – all of which is potentially catastrophic to hydraulic systems.
Testing Hydraulic Fluid Contamination
For hydraulic equipment to remain in good order, it should be regularly tested for contamination according to the manufacturer’s recommendation. Additionally, contamination checks should be carried out whenever contamination is suspected, or when the system has been operating at unusually high temperatures. A thorough contamination check involves taking more than one sample of the hydraulic fluid in different locations (for example the fluid reservoir and other locations), allowing you to track down the source of the contamination. Identifying and addressing the cause of the hydraulic fluid contamination is crucial to prevent the inevitable breakdown and increased repair costs.
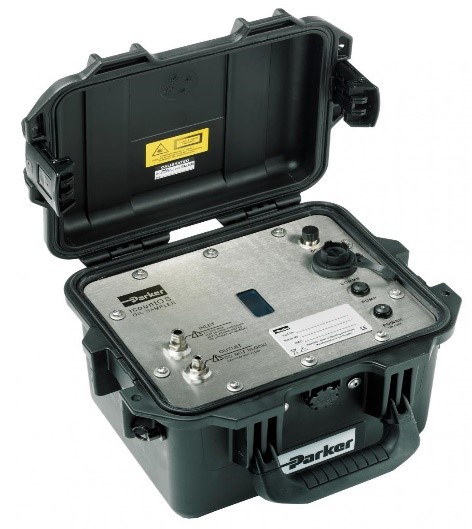
Preventing Hydraulic Contamination
Filtering is essential to prevent hydraulic contamination. All fluid should be filtered through a fluid service cart or unit before it is transferred to a hydraulic system and/or components. Filters should be checked, cleaned, and replaced per manufacturer guidelines. We advise using those recommended by the manufacturer and to avoid cheap, low-quality filters. Filters should only be removed from their packaging, in a clean environment, immediately before use and handled carefully to reduce the risk of contamination.
Take samples before flushing original fluid and again when adding the new fluid. Remember to also change filters. Depending on the results from the samples, filters and fluids may need more often.
Another way to prevent hydraulic fluid contamination is by keeping a clean work environment. Only lint-free cloths should be used and workbenches, tools and servicing equipment kept clean to minimise the risk of contamination. Whenever disconnecting hydraulic fittings or lines, the workspace and all components should be cleaned in an approved dry solvent, dried (with a lint-free cloth, as needed), and then lubricated before assembly takes place. Always use dust caps on the ends of couplings when they are not in use.
Hydraulic Oil Analysis with Rotec Hydraulics Ltd
As well as offering an expert maintenance, repair and overhaul service, Rotec Hydraulics Ltd is proud to offer the Parker icount Oil Sampler (IOS) – a portable condition monitoring for hydraulic oil and fuel systems.
IOS is an innovative solution to measuring the quality of hydraulic oils and hydrocarbon fuels. Lightweight, robust and portable, IOS features a laser detection particle counter, battery and pump plus memory with web page generator for data download onto any PC or laptop – enabling clients to sample oil on-site and gather results within 5minutes. The IOS’s ability to sample directly from a hydraulic reservoir, barrel, vehicle fuel tank or from a high pressure online hydraulic system with the addition of a pressure reducing adaptor makes it undoubtedly the most adaptable contamination service tool available today. Contact us today for more information.