Rotec Deliver Vessel Overhaul at A&P Falmouth
Rotec’s Electrical Mechanical Services team have recently carried out significant maintenance and overhaul works on the vessel Norbay at A&P Falmouth.
Originally built in Rotterdam in 1994, Norbay and her sister Norbank were two of the first of a new generation of ‘super freighters’. The vessel is currently used as a car, passenger and freight ferry in the Irish Sea for P&O Ferries.
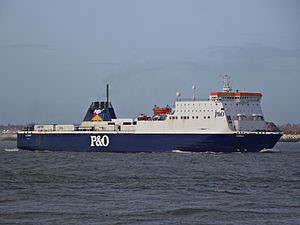
Specialists in alternators and generators, Rotec’s Electrical Mechanical engineers have completed a significant overhaul project on the vessel Norbay, on-site at A&P Falmouth. The work included:
- On-site Aft Bow Thrust Overhaul inc. internal inspection, replacement bearings, rebuild, testing and full works report
- Port Alternator Clean and Bearing Change
- Main Vehicle Deck Aft Cargo Fan Overhaul inc. collection from dockside to Rotec workshop inspection, steam clean, re varnish, new bearings, dynamic balancing, testing and reinstall
- Cargo Fans motors overhaul.
The work carried out will ensure the continued performance and availability of the vessel. Greg Sandy, Business Development Manager and part of Rotec’s Electrical mechanical Services team said:
“Rotec are proud of their strong relationship and partnership with A&P Group in Falmouth, which sees us providing quality services and solutions.
“Our extensive range of services and products, combined with the experience and knowledge of our technical team has given us the well-deserved reputation for being a trusted provider of quality Electrical Mechanical Services.”
Rotec have been trading for over 30 years and take pride in delivering project specific solutions, sustainable results and added value to their clients. For more information on our Electrical Mechanical Services offer, click here.
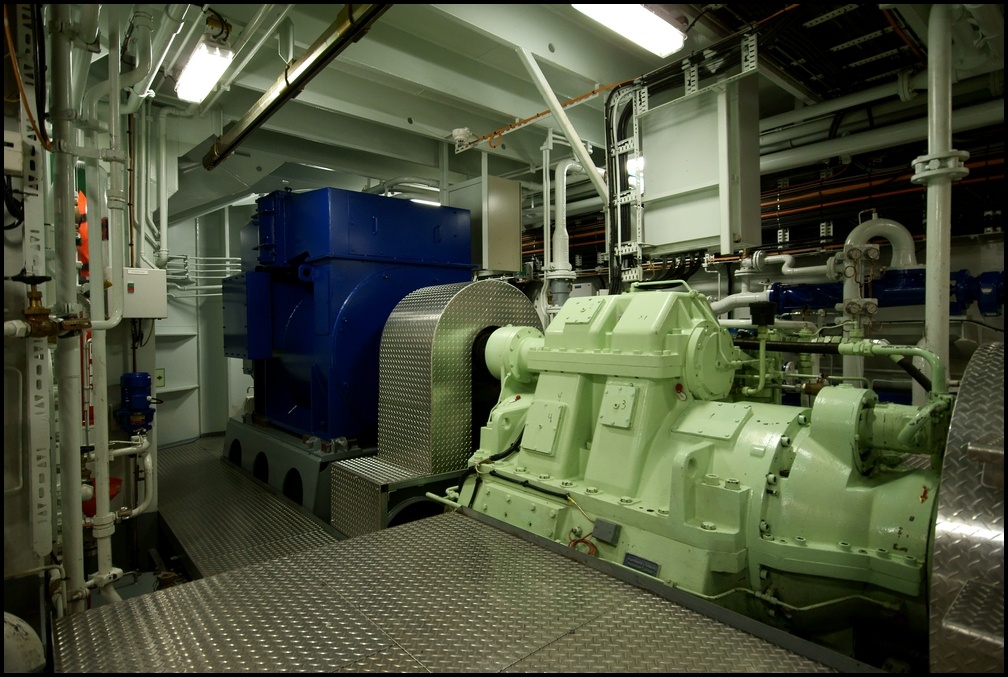